SUBCONTRACTOR BUYS SLIDING-HEAD LATHEĀ FOR HIGH PRODUCTIVITY AND “AN EASY LIFE”

These days when turning and milling components less than 38 mm in diameter, it is difficult to justify using a fixed-headstock CNC lathe, such is the high level of capability, productivity and flexibility of modern sliding-head turning centres (sliders). This is the view of Martin Lock, owner of 55-years-established subcontract machining firm PES Engineering, Burnham-on-Crouch, who took delivery of a Cincom L32-XLFV slider from Citizen Machinery UK (www.citizenmachinery.co.uk) in April 2022.
He said, “We held off investing in this technology before, as up to about five years ago sliding-head lathes were not as flexible as their fixed-head counterparts in terms of their power or the number of tools in the working area. Consequently they could not produce such a wide variety of components, but that is no longer the case.
“Modern sliding-head lathes are able to produce anything a fixed-head equivalent can, and on average completes the same cycles in two-thirds of the time. It is down to the speed of movement of the gang tooling and the wealth of static and live cutters that can be deployed.”
Chipbreaking software is a game-changer
PES Engineering has over the years developed a reputation for supplying components in small to medium size batches, typically 3,000- to 5,000-off. Larger quantities are often produced and stocked at Burnham-on-Crouch for Kanban call-off by customers. Materials range from stainless steels, which account for half of throughput, to plastics, which make up another 20 percent. Both tend to generate stringy swarf when machined on the subcontractor’s fixed-head lathes.
Swarf invariably wraps around the tool and the component being machined, risking damage and prematurely wearing the cutting edge of the carbide inserts. Feed rates have to be reduced to mitigate abrasion, lowering production output. Furthermore it is generally necessary to stop a lathe regularly to remove the swarf, making light-outs running virtually impossible unless a free-cutting material like brass is being processed. All of this negatively impacts productivity and profitability.
Such problems are not encountered on the Cincom slider, as it is equipped with Citizen’s programmable low frequency vibration (LFV) software in the operating system of the Mitsubishi control that breaks the swarf into smaller chips. Launched five years ago, the three modes of LFV developed to improve turning, grooving, drilling, boring, threading and parting-off not only avoid bird’s-nesting, but also reduce or eliminate the need to use expensive and energy-hungry high pressure coolant equipment.
Mr Lock continued, “LFV has removed much of the aggravation of turning stainless steels, which gives us a much easier life. We can machine efficiently everything from 304, which is billed as free-cutting but really is not, through to highly alloyed marine grades.
“With LFV, oscillation of the spindle relative to the axis feed motion momentarily and repeatedly lifts the tool clear of the component surface. It has the effect of breaking the swarf before it has a chance to form a string and also lowers the temperature at the point of cutting, reducing work hardening of the metal and preventing built-up edge on the insert.
“We have LFV switched on permanently when machining plastics and it works perfectly, even on nylon. When processing stainless steel, for nine out of 10 components we produce it is engaged for typically half of the cycle and always for parting-off. Programming the function to stop when it is not needed limits the milliseconds of slightly decreased metal removal rate when the tool is air cutting.”
Strategies that Mr Lock previously used to control swarf length included introducing peck feeding and dwells, which extended cycle times and accelerated tool wear, and experimenting with different chipbreaker designs on the insert. None of this is needed any more, as he says most materials chip like brass simply by selecting cutting parameters out of Citizen’s LFV manual.
Purchasing decision
At the end of last year, two 40 mm capacity fixed-head lathes producing 304 stainless steel medical parts broke down on the same afternoon, prompting Mr Lock to look for a replacement. As sliding-head technology had advanced sufficiently to consider it, he decided to go down this route. He was in regular contact with another subcontractor with which he occasionally shares work, and that company operates 10 Citizen lathes including LFV Cincoms that have proved to be reliable and accurate over the years. Once a machine is warmed up and set, tolerances do not move and machining to within microns is routine.
It therefore made sense for PES Engineering to opt for the Citizen brand. An L32XLFV was duly ordered with a conversion kit that allows stock up to 38 mm diameter to be fed from an Iemca three-metre bar magazine. Immediately apparent was the sheer speed of the machine, with many parts coming off more than twice as quickly compared with the output from one of the ageing fixed-head lathes. In one extreme case when turning a plastic part unattended, 400-off were produced in two hours instead of over a full manned shift.
Two tools can be in cut simultaneously on the slider for high levels of productivity. Moreover the latest-generation L32 type X has a Y2 axis on the sub spindle, allowing cutting operations to be shared more evenly between it and the main spindle, minimising cycle times.
In the first three months of operation, the L32XLFV produced 20,000 parts of around three dozen varieties, all but one of which were in length less than 2.5 times the diameter. The majority were therefore not classical sliding-head work, so Mr Lock plans to take advantage of the ability on most Cincoms, including the L32, to remove the guide bush. The main advantages are the ability to use less expensive bar, as straightness and dimensional variation are not so much an issue, and a four-fold reduction in remnant length at the end of each bar, leading to significant material savings.
The Cincom is not only the first slider that Mr Lock has bought, but it also represents the first time he has dealt with Citizen Machinery UK. He has been impressed with the supplier’s service, which he describes as “refreshing”.
He added, “We have had fantastic human interaction and service from everybody in the company, from the sales team through ordering, machine installation and commissioning to service back-up.
“If we email or phone Citizen’s service department, we receive a call back in half an hour – sometimes within a couple of minutes – something other suppliers never seem to do in our experience.
“With the Cincom being our first slider, we were reliant on prompt and comprehensive telephone advice at the outset and still are to some extent. It has proved invaluable.”
About PES Engineering
Established in 1967 by Mr Lock’s father Clifford and a partner who subsequently left, PES Engineering (www.pesengineering.co.uk) derives its turnover from milling and turning in approximately equal measure. Industries served are mainly aerospace, automotive, medical, hydraulic, rail and electronic connectors, and customers are to be found throughout the UK as well as in the US and Germany.
A particular specialism is design for manufacture, i.e. redesigning components to simplify their manufacture and reduce the cost of production, while maintaining the part’s full functionality in service. In one recent case, an injection moulded plastic component that was proving difficult for a US customer to assemble with other parts was re-engineered so that it could be turned from plastic bar at an acceptable price. The result was highly satisfactory and the contract is ongoing.
In conclusion, Mr Lock observed, “Automating the turning side of our business using a bar feeder is much easier, cheaper and less space consuming than retrofitting one of our machining centres with robotic machine tending.
“So I decided that investment in autonomous turning and milling of components in one hit was the way forward and it is proving to be the right choice.
“We will now progress to turning on the L32 without the guide bush for all but the longest shaft-type components, which are rare orders for us at the moment as we are not known as a sliding-head shop, but of course we are now in a position to fulfil that work.
“The expectation is that we will also use the Cincom for machining purely prismatic parts with no turning at all apart from parting-off, which will go some way to automating production of some of our milled parts as well.”
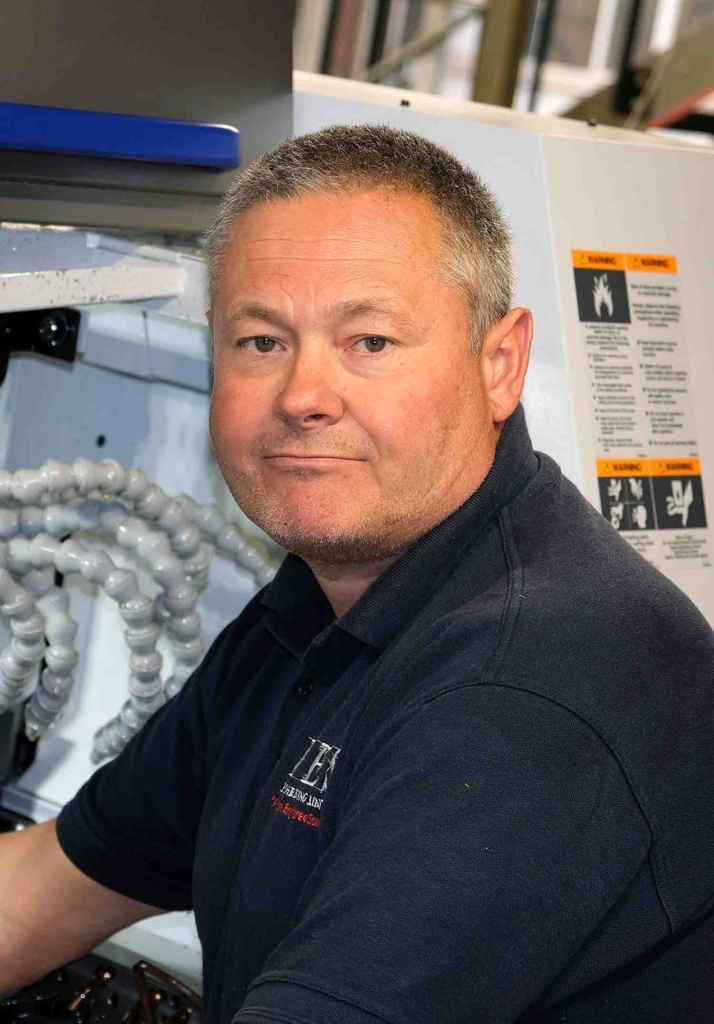
Martin Lock, Owner, PES Engineering.

The Citizen Cincom L32-XLFV sliding-head mill-turn centre on the shop floor at subcontractor PES Engineering, Burnham-on-Crouch, being operated by owner Martin Lock.
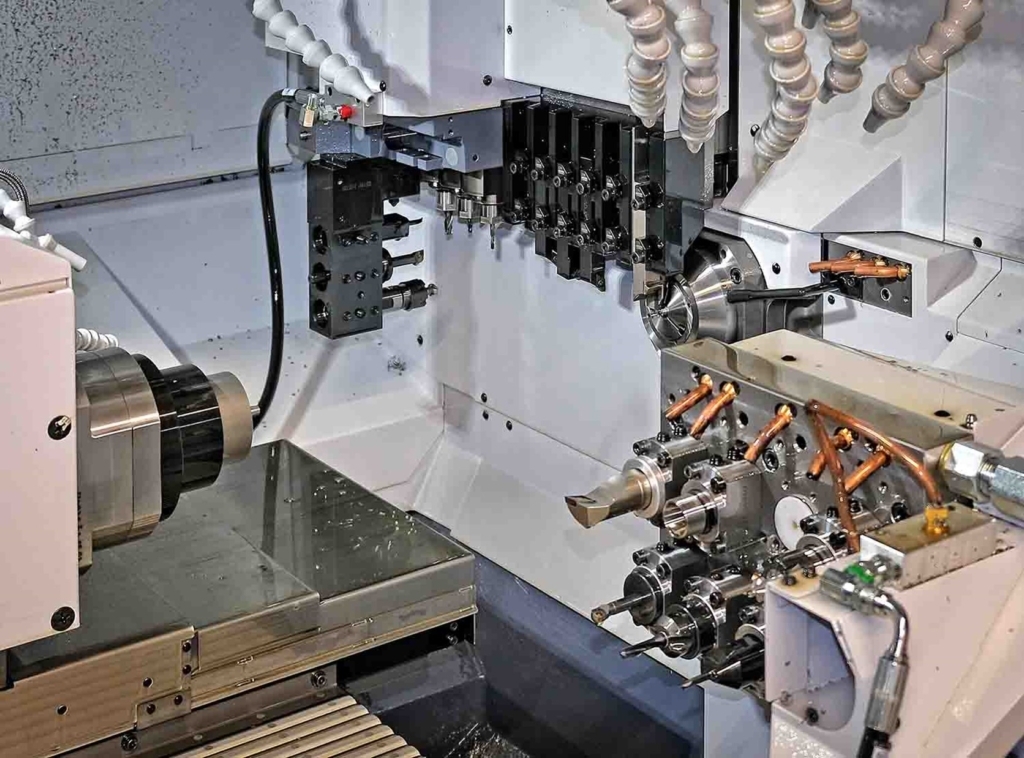
The machining area of the L32-XLFV that
Mr Lock describes as spacious and flexible.
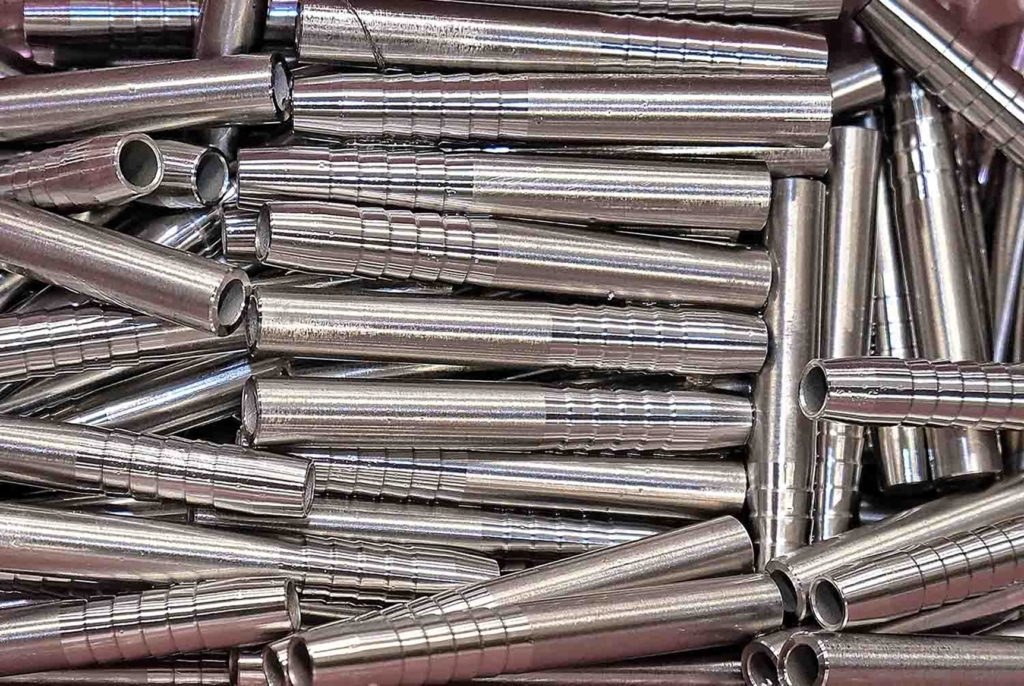
BSP hose tail outlets machined from 304 stainless steel bar on the L32-XLFV
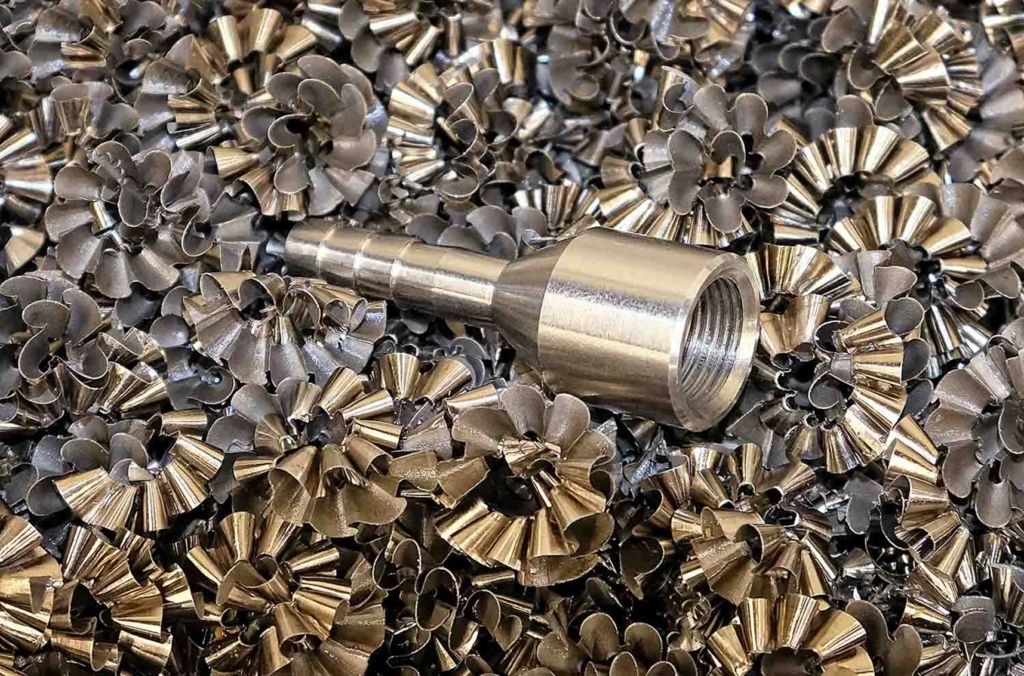
A 304 stainless steel BSP hose tail inlet machined from larger diameter bar on the L32-XLFV. Pictured around the part are the short, manageable chips that result when OD turning with Citizen’s low frequency vibration software.
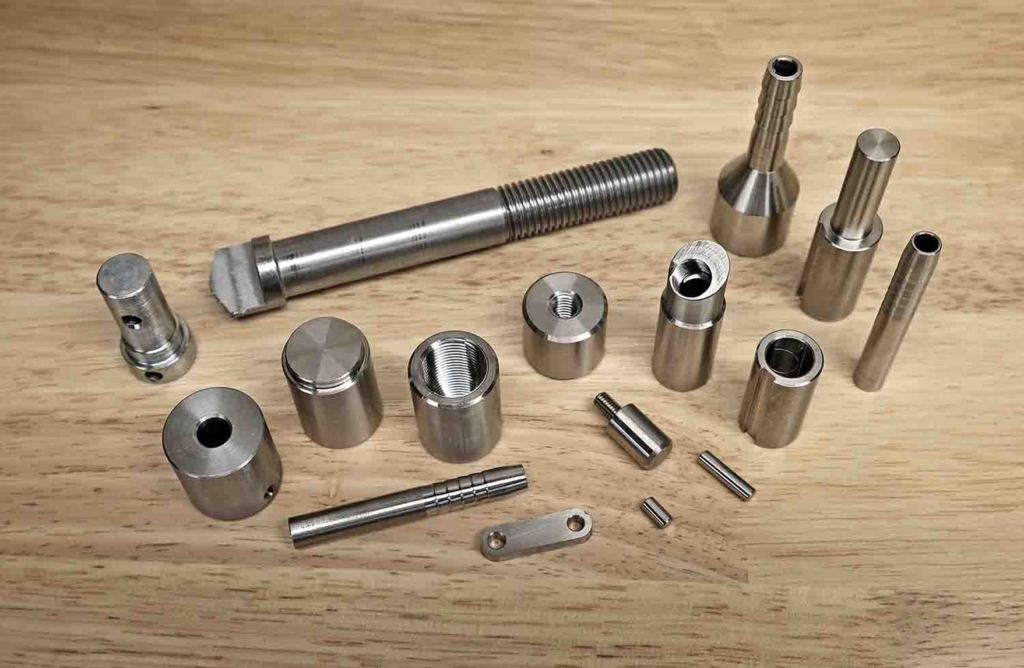
A selection of components machined by
PES Engineering in one hit on the L32-XLFV.
On behalf of:Ā Ā Ā Ā Citizen Machinery UK Ltd,
1 Park Avenue, Bushey, WD23 2DA.
Tel: +44 (0)1923 691500.
Contact: sales@citizenmachinery.co.uk
Website: www.citizenmachinery.co.uk
Issued by:Ā Ā Ā Ā Ā Ā Ā Ā THE RIGHT IMAGE Ltd
PO Box 42, Twickenham, TW1 1BQ
Tel: +44 (0)20 8891 0603
Contact: Chris Wright
Email: chris@therightimage.net
Website: www.therightimage.net
Release no:Ā Ā Ā Ā Ā Ā 1181(CS)